Liquid Technologies
Thermal Processing Solutions for Food and Beverage R & D
MicroThermics Lab Scale HTST/UHT Equipment
MicroThermics small scale HTST/UHT Thermal Processing equipment is designed with flexibility and ease of use to process production quality samples for a wide range of products such as flavoured milks, plant based beverages, protein shakes, meal replacements, juices, sauces using a range of thermal processes Aseptic, ESL, HTST by Indirect Heating or Direct Steam Injection. Our engineers can adapt design features to meet a customer’s unique requirements, whether related to specific product characteristics or in-house bespoke thermal processes.
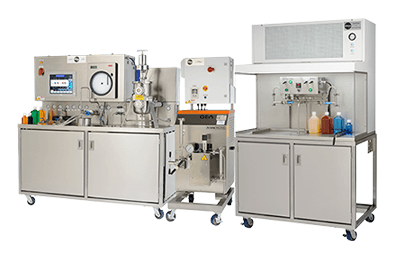
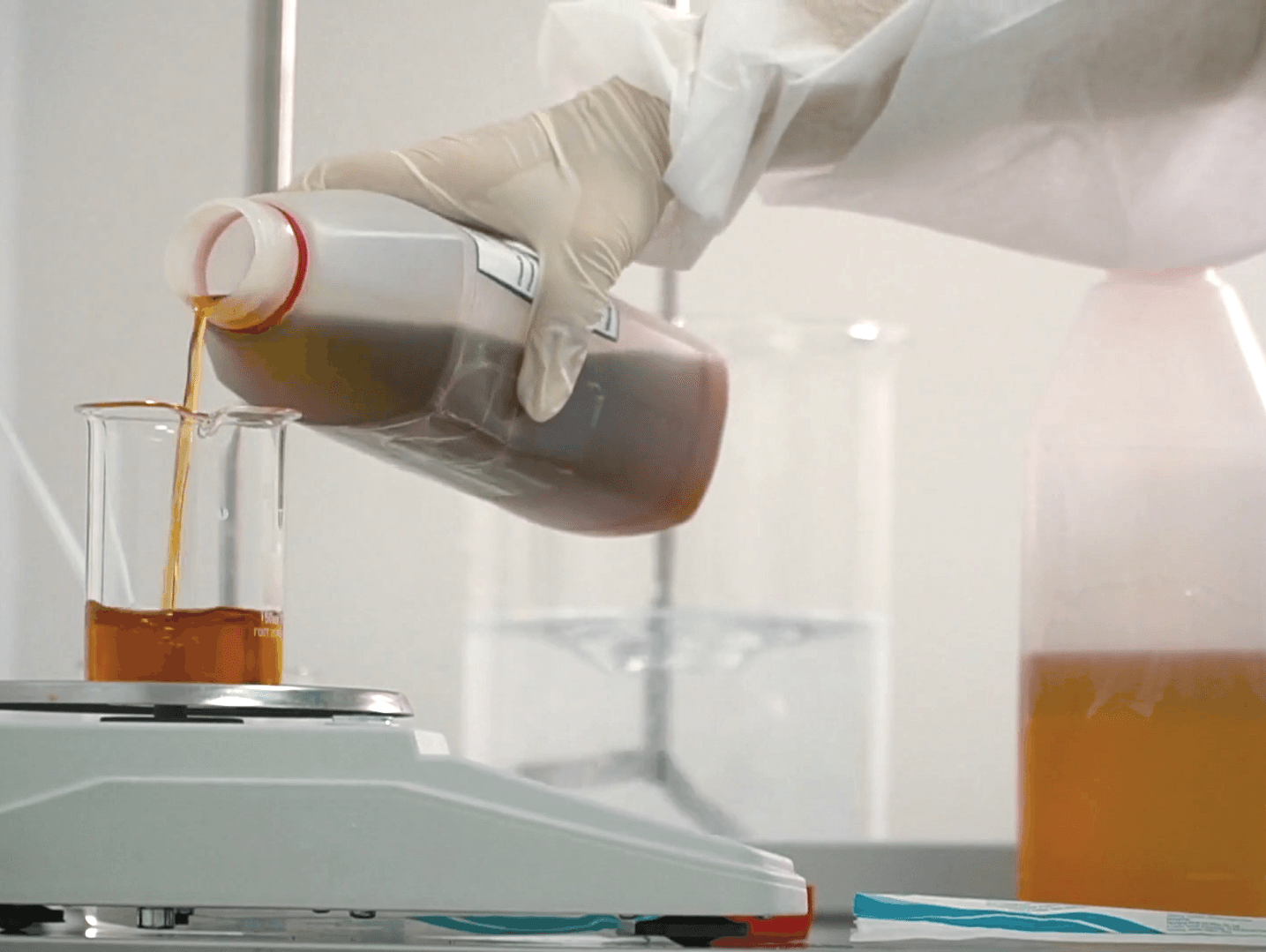
Processing Technologies for Product Developers
- Indirect Heating with Tube in Shell or Plate Heat Exchangers -
- Direct Steam Injection
- AI Indirect Series Processor has a Full Automation Package for Ease of Use and Enhanced Operator Efficiencies
- Check out the virtual show-room https://microthermics.com/virtual/
- Inline High Pressure Homogenisation
- Ultra Clean Laminar Air Flow Cabinet for container/bottle filling
- Extra Hold Tube options
- Additional Cooling Heat Exchangers
- Rapid Sterilisation Option
- Capability to design and build for specific client requirements
MicroThermics HTST/UHT Specific Equipment Functionalities
Onboard software provides a range of tools to ensure ease of use, accuracy and repeatability of sample processing conditions and retention of processing records by way of:
- HMI Touchscreen PC and PLC control
- Alarms Package
- Sensor Calibration Package
- Product Recipe and Processing Parameters Data Storage
- Data Logging of Process Parameters with extraction to USB Storage Device or Local Network
- Range of Control Safeties including hard wired and software safeties
- eConnect Option for Controlled Cloud Connectivity - used for Software Updates, Technical Support and Troubleshooting
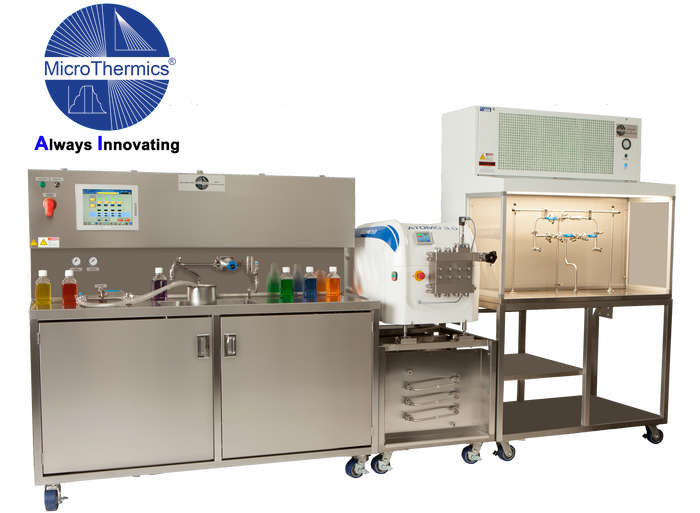
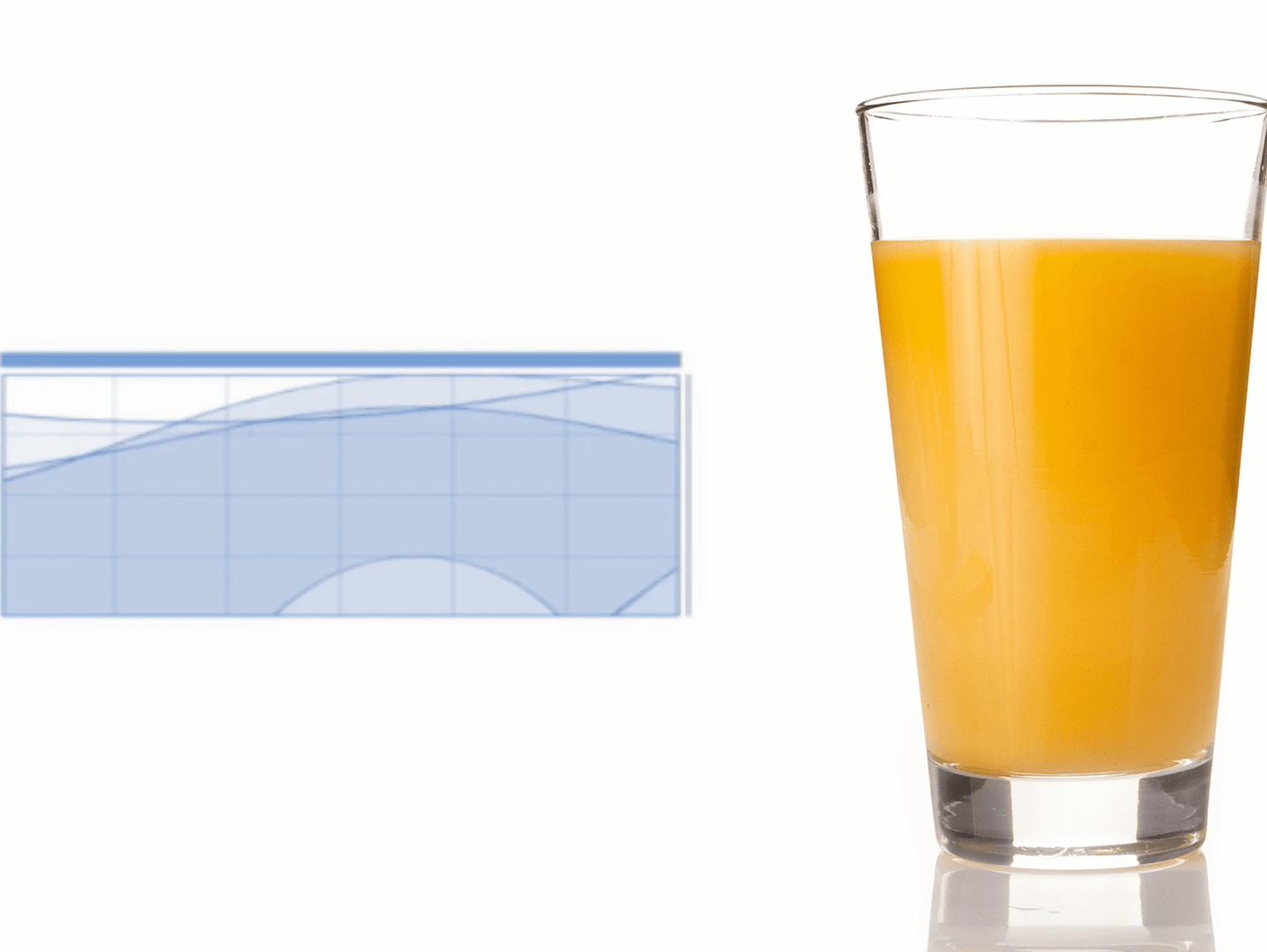
Benefits of MicroThermics HTST/UHT Processors
- MicroThermics Lab scale Thermal Processors are accurate across the entire thermal process thus preventing failure of products when transferred to production.
- Product Development cycle time is reduced thus getting products to the market quicker
- Process sample quantities to accurately match plant processing conditions
- Reduce new product development cost. Test more formulations.
- Have more new products in the development pipeline